In the ever-evolving landscape of 3D printing with copper offers new opportunities for diverse range of sectors. From advanced heat sinks to customized electrical parts and biocompatible medical implants, the potential applications of 3D printed copper are vast and groundbreaking.
In this article by Innovana3D we will understand application, advantages and challenges of 3D printing copper, with context of metal additive manufacturing.
Potential Applications
- Heat Sinks for Next-Gen Electronics: The ability to create intricate internal channels through 3D printing enables the production of heat sinks that excel in superior heat dissipation. This innovation is poised to elevate the performance of next-generation electronics, ensuring efficient temperature management.
- Custom-Designed Electrical Components: 3D printing allows for the creation of lightweight, custom-designed electrical components. With optimal conductivity and reduced size, these components promise improved efficiency and functionality, catering to the ever-shrinking demands of modern electronics.
- Biocompatible Medical Implants:The biocompatibility of copper makes it an excellent choice for medical implants. Through 3D printing, customized implants with improved tissue integration and enhanced bone healing properties can be crafted, ushering in a new era of medical advancements.
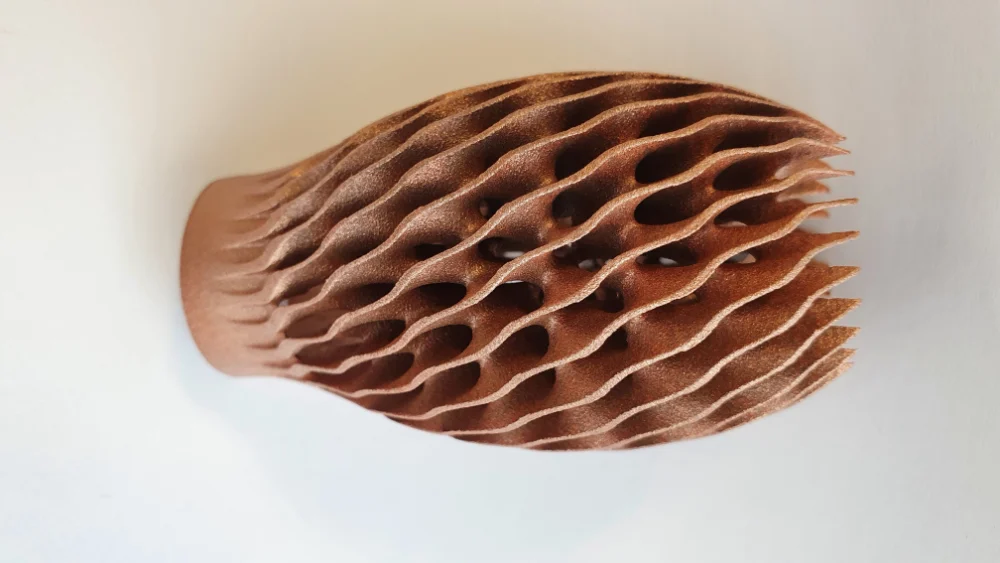
Key Benefits
- Unmatched Conductivity: Copper stands out with its exceptional electrical and thermal conductivity, making it the metal of choice for applications requiring efficient heat transfer and current flow. This quality positions 3D printed copper as a frontrunner in the realm of high-performance materials.
- Geometric Freedom: Unlike traditional manufacturing methods, 3D printing provides the freedom to create complex geometries with internal features and intricate details. This capability pushes the boundaries of design, allowing for the production of components with unprecedented intricacy.
- Lightweighting Potential: 3D printed copper parts exhibit the potential to be lighter than their traditionally manufactured counterparts. This characteristic is particularly advantageous in sectors such as aerospace and automotive, where weight reduction leads to enhanced efficiency and fuel savings.
- Material Efficiency: Techniques like binder jetting and Metal FDM minimize material waste, a significant advantage over traditional subtractive methods like machining. This not only contributes to cost-effectiveness but also aligns with sustainable manufacturing practices.
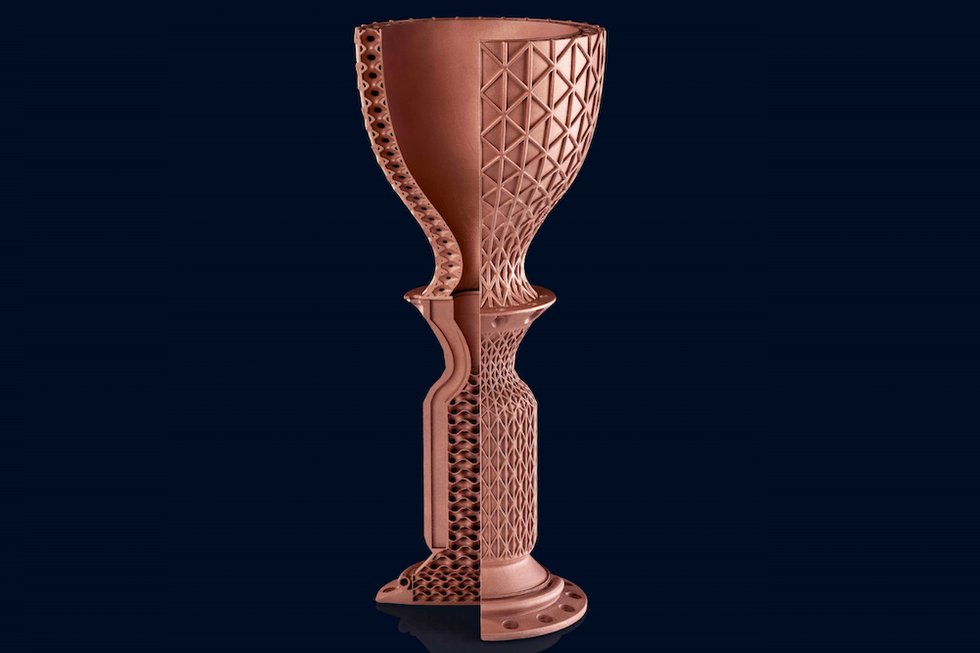
Challenges
- Cost: The current stage of 3D printing with copper comes with its challenges, including the relatively high cost of materials and equipment. However, as the technology matures and gains wider adoption, the associated costs are expected to decrease.
- Post-Processing Requirements: Depending on the chosen printing method, post-processing steps such as sintering or polishing may be necessary for optimal performance. These additional processes contribute to the overall production timeline and complexity.
- Support Removal: Certain 3D printing techniques for copper necessitate support structures that require careful removal, adding an extra layer of complexity to the manufacturing process.
Conclusion
In conclusion, the potential of 3D printed copper is significant for various industries. While challenges such as cost and post-processing requirements persist, the continuous advancement of technology is expected to make 3D printing with copper more accessible and widespread. As we stand on the cusp of this transformative era, the question arises: are you ready to embrace the future of manufacturing with 3D printed copper? Share your thoughts with us.